Intelligent fault detection for efficient production processes
Checking metal objects in production, processing or goods control environments often means that parts have to undergo time-consuming visual or manual inspections, and expensive equipment may also be involved. The Marquise project, established by Fraunhofer CCIT with a focus on magnetic field-based quality control, is developing a solution to this in the form of a system that performs automated inline quality control on conductive objects in the production process. It uses what is known as the magnetic fingerprint of objects to detect production faults with the assistance of AI technology, resulting in efficient, cost-effective quality control during operation.
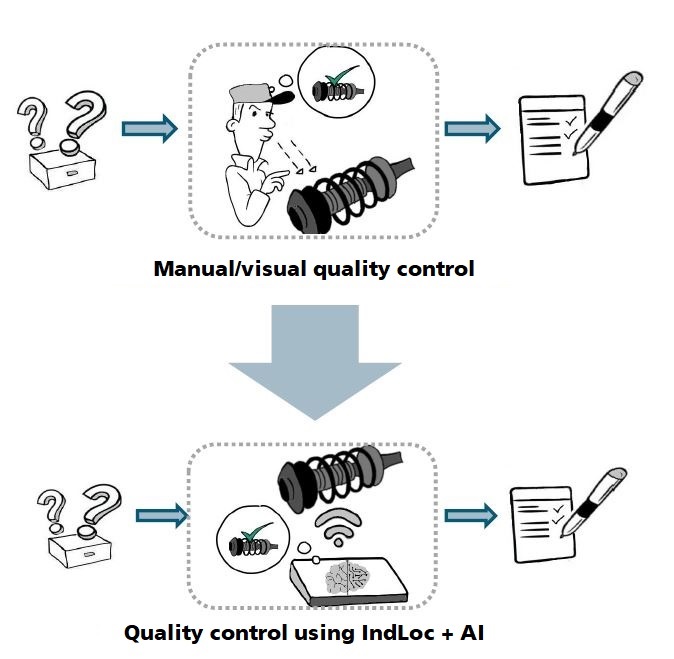
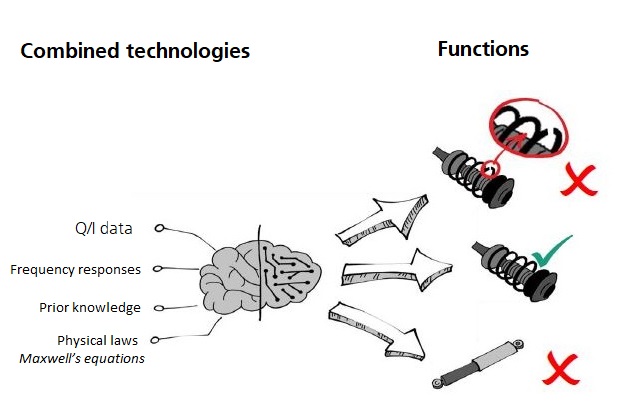
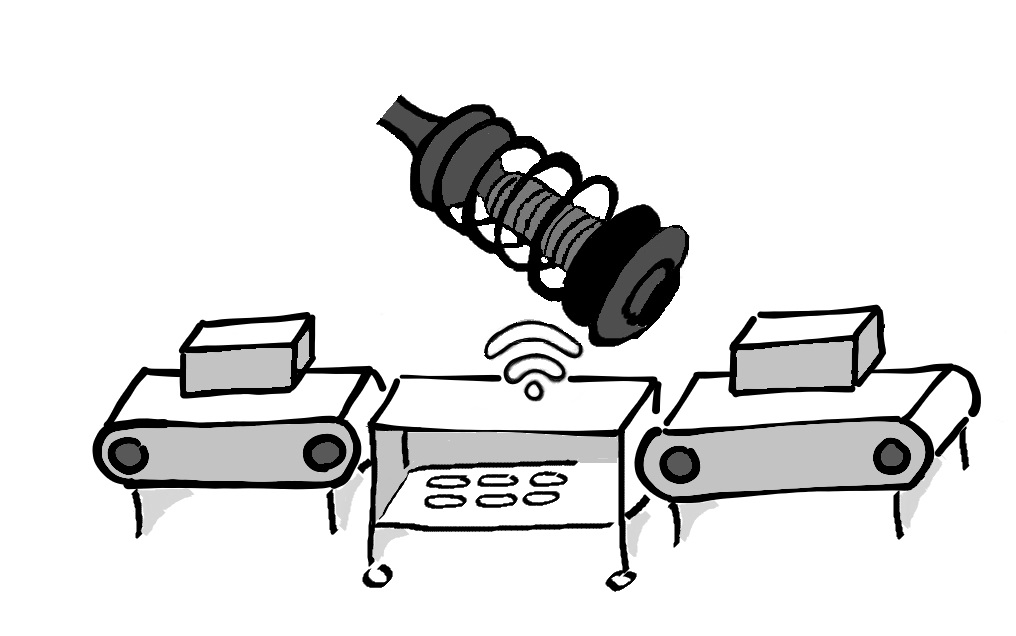
The system identifies and distinguishes between different metal objects, and automatically detects production faults and defects that are difficult to identify visually, such as missing details, holes or structural issues. It is able to analyze even complex structures including smart meters and die-cast aluminum body parts without the need for additional markings or identifying features such as barcodes or transponders.
The object control process is based on the magnetic fingerprint of the part being checked — something that is generated by means of secondary fields that arise when conductive objects in an alternating magnetic field are excited at various frequencies. Working on the basis of this data, AI algorithms are used to differentiate between faulty and non-faulty objects, and separate out defective items directly within the production process.
This magnetic field-based quality control method can be integrated effortlessly into existing production lines, is easy to operate and has a straightforward structure that makes it less expensive than comparable methods involving X-ray systems, which require additional protective measures to guard against dangerous radiation. In contrast to visual inspection methods performed by optical systems, the quality of the data that is captured is not affected by dust, light conditions or packaging. Even when it encounters objects stored in boxes, the system is able to provide direct feedback on the properties of the contents. This allows for instant quality control during operation in the context of manufacturing or processing metal C-parts produced in large quantities, and even during inspections on incoming goods, outgoing goods and returns.
Integration of two Fraunhofer technologies
The research project is combining the expertise of two Fraunhofer institutes in the processes of positioning and material detection on the basis of magnetic fields, and in the use of artificial intelligence to optimize complex processes, making it possible to perform quality control efficiently and with maximum accuracy.
The Fraunhofer Institute for Integrated Circuits IIS is responsible for the data acquisition component of the project. For this purpose, its researchers are using IndLoc® technology: a highly precise, real-time-capable 3D localization system that performs localization and sensor-based functions using low-frequency alternating magnetic fields. When conductive objects such as screws or shock absorbers are excited in an alternating magnetic field, secondary fields are generated at various frequencies. The secondary fields vary according to the material and geometric properties of the objects. Providing unique signatures for the objects, they are compared with reference values and enable precise localization and material detection.
Using technology of this kind in real-life industrial processes requires powerful, AI-based data processing that enables object detection and can accommodate strategies for learning about new objects. This is where the Fraunhofer Institute for Intelligent Analysis and Information Systems IAIS comes in through its role in using features identified in data sets to develop AI algorithms for detecting and distinguishing between objects. Insights into signal processing and physical laws governing magnetic fields are incorporated in order to perform data-efficient training, with the aim of achieving outstanding object classification abilities. As an example, the algorithm can even differentiate between extremely similar objects that approaches such as conventional computer vision methods would find it difficult to separate.